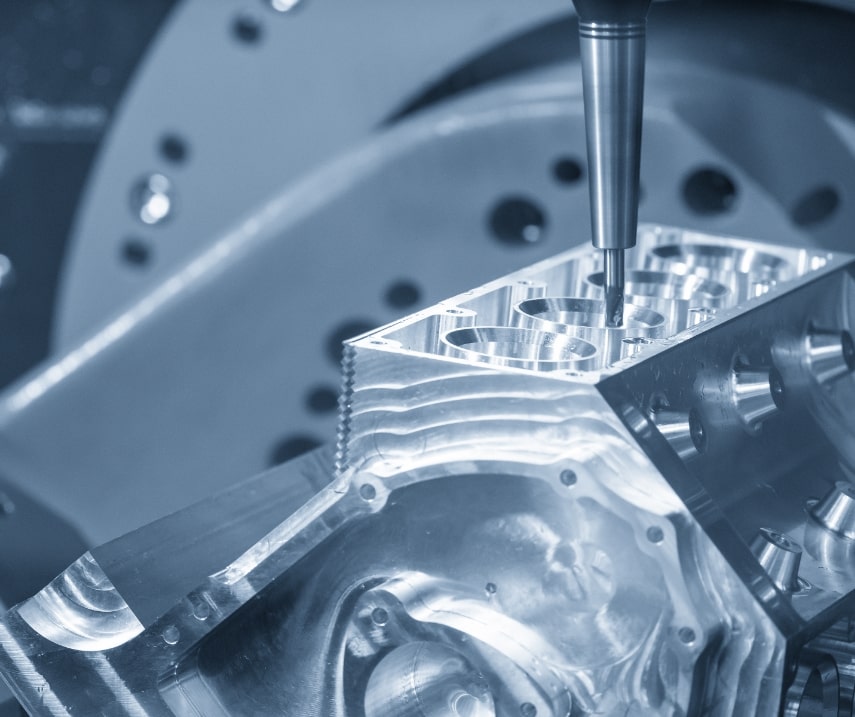
Die casting has become an integral part of Malaysia’s manufacturing sector, playing a critical function in sectors such as electronic, automotive as well as consumer goods. Die casting involves the injection of the molten metal in a mold with high pressure in order to make precise and durable components. Through the years, Malaysia has emerged as one of the top players in the industry of die casting because of its technological advancement, highly experienced workforce, and low manufacturing costs. Its location in the middle of Asia and strong infrastructure have attracted global manufacturers looking for quality and reliable die-cast parts. The demand for light and long-lasting metal components is increasing, Malaysia’s die casting industry is poised for further expansion which will significantly boost the economy of Malaysia.
Die casting in Malaysia is embracing technological advances in order to improve efficiency and accuracy in manufacturing. Companies are investing in high-tech technology, machinery along with computers-aided design (CAD) software to increase the accuracy and consistency of die-cast products. Modern die casting techniques allow manufacturers to produce complicated parts that require minimal waste which reduces production costs as well as the environmental impact. Many Malaysian die casting companies are also integrating sustainable practices, such as making use of recyclable materials as well as increasing energy usage. With the adoption of new production techniques, Malaysia is strengthening its standing as a source of high-end die-cast products while meeting the international standards for sustainability and quality.
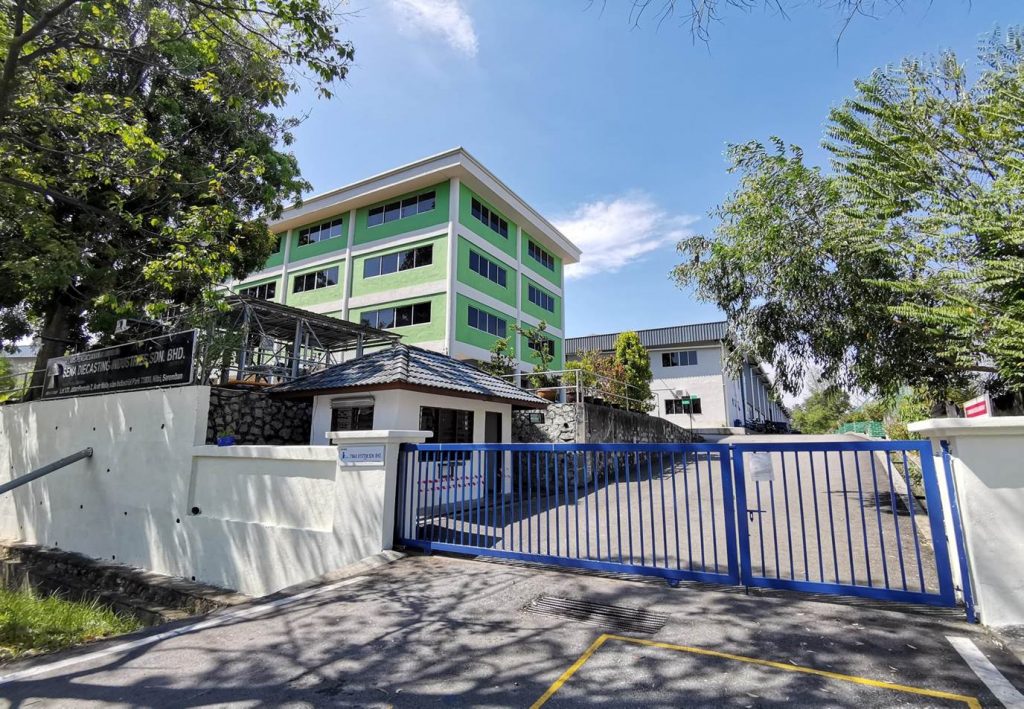
The automobile industry is one the main drivers for Nickel chrome plating Malaysia industry manufacturing companies relying on die-cast aluminum and zinc components to make vehicles. Lightweight metals are crucial in automotive manufacturing today aiding in improving performance and efficiency in the combustion process, as well as reduce emissions. Die-casting components such as engines transmission casings, engine blocks, and structural components play a vital role in the performance of vehicles and their safety. As the popularity of electric automobiles (EVs), the demand for precise die-cast parts is growing as car manufacturers look for lightweight materials that can improve battery performance. Malaysian die-casting companies are adapting to these changes by refining their production techniques and expanding their capacity in order to cater to the increasing EV market.
Beyond the automotive industry, Malaysia’s die casting sector is also used to serve consumers and electronics marketplaces. Electronics industry is heavily dependent on die-cast products including laptops, smartphones as well as home appliances. These components provide structural integrity whilst keeping devices light and small. Malaysia’s role as a leading actor in the global manufacturing of electronic components has created a high demand for die-cast parts which meet the strictest performance and durability requirements. Manufacturers of consumer goods also profit of die-casting technology which produces top-quality metal parts that are used in household products, tools, and industrial equipment. With advancements in technology, and as product designs become more intricate so the requirement for high-quality die casting will continue to increase.
Despite its rapid growth, the die casting industry in Malaysia faces problems such as changing price of raw materials as well as rivalries from manufacturing hubs within Asia. Costs of aluminum and zinc alloys can impact production expenses and make cost-efficiency an important consideration for companies. In addition, competing against large-scale production companies of China as well as India demands Malaysian firms to concentrate on innovation, quality control as well as customer satisfaction. To stay competitive, many Malaysian die casting companies invest in research and development, enhancing their manufacturing processes, and giving customers customized solutions. Industry collaborations and support from the government also play a key role in strengthening the sector by increasing technological innovation and the growth of workers.
The future of die-casting in Malaysia looks promising, driven by the growth of industry, technological advancement, and the growing global demand for high-quality metal components. With more businesses embracing Industry 4.0 technologies such as robotics, artificial intelligence, along with data analytics, efficiency and quality of die-casting process will only enhance. The sustainability efforts will influence the future of die casting, with manufacturing companies adopting green techniques and developing recycled materials. With its strong manufacturing foundation and commitment to innovation Malaysia is expected to stay an important participant in the world’s die casting industry. The industry’s continuous evolution will not only contribute to prosperity but will also cement Malaysia’s standing as a dependable and forward-looking manufacturing hub.